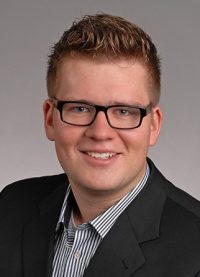
Laser Pre-Treatment and the Future of Hybrid Materials
Interview by Liliana Caldero
Originally in LIA TODAY July/August 2019.
Throughout the world, scientists are rising to the challenge of developing new techniques to improve the eco-friendliness of products and production lines. Germany has been among the strongest supporters of the movement to be more environmentally responsible. Innovations resulting from this momentum may lead to more efficient manufacturing, which could ultimately cut costs without compromising quality. Hybrid materials are growing in importance in the search for strong, lightweight materials that produce fewer CO2 emissions. Dominic Woitun of the German-based Bosch is among the researchers investigating techniques for effective thermal direct joining of hybrid materials. Joining dissimilar materials such as metals and plastics can pose a challenge; this challenge is often solved with the use of adhesives or screws with sealants. Adhesives may work, but according to Woitun, they leave a larger carbon footprint. This is where thermal direct joining comes in. The process that Woitun is researching involves using laser ablation to shape macroscopic structures into a metal surface; the structures are then penetrated with a molten polymer which enables mechanical fastening, for instance. After solidification, a strong joint is obtained, which replaces the need for an adhesive. The shapes, or geometries, created by the laser play an important role in the strength and reliability of the joint, so better understanding the relationship between these geometries and the resulting joint will help make this a viable alternative to adhesives. Woitun shared with LIA TODAY why he started researching the impact of laser geometries on thermal direct joining of hybrid materials, and why companies could consider this an answer to adhesives.
LIA: For some in our community, the term ‘thermal joining’ brings to mind laser welding of metals; for those who are new to the concept of thermal direct joining of hybrid materials, could you describe what this process can look like, step-by-step?
DW: Thermal direct joining is a joining technique for metals and polymers. The adhesive forces of a thermoplastic melt to metals is used to join both partners. No additional adhesive is needed. However, to achieve strong joints, some form of surface pretreatment is needed. Laser structuring is a promising approach.
The process steps to a finished part could look like this:
- Preparation: prior surface treatment (e.g. by laser ablation)
- Joining: Many different techniques are possible! The only premise is a somehow molten polymer in the joining interface that can penetrate the structure. This can be achieved, for example, by heating the metal part with some kind of heat source and then pressing it onto the plastic part. Or, in my case, by using injection molding and overflowing the metal part with molten polymer in the molding tool.
- Finishing: the molten polymer solidifies instantly and directly after joining the joint has almost its final strength
LIA: Tell us about what drove you to research thermal direct joining?
DW: In order to meet today’s requirements for weight reduction and thus emission reduction, hybrid components are becoming increasingly important. Especially in the context of electrification. One main challenge for the production readiness of hybrid composites is the joining technology. Currently, hybrid parts are often joined by adhesives or screws in combination with sealants. Therefore, the interfaces need to be handled with special care and must be cleaned before joining. After joining, the parts need a certain curing time before they can be further processed. When it comes to recycling, there is almost no way to separate the often used and recyclable thermoplastic material from the duroplastic adhesives. This makes the current solutions time-consuming and costly.
LIA: What are you researching right now and how does it help to solve these challenges?
DW: Direct joining of metals and polymers based on a laser-pretreatment bypasses these problems and produces strong and media tight joints directly after the joining process. However, the enormous variety of laser sources, in combination with their adjustable parameters, open up endless possibilities for structures on the metal surface. This often ends in time-consuming empirical studies to find the best settings for one specific use case. That’s why I’m investigating the influence of largely separated surface characteristics on the joint properties by generating well-defined structures on the metal surface by laser ablation. My aim is to find the best weighting and composition of surface characteristics to define the optimal structure for an application.
LIA: What benefits could companies gain from utilizing direct joining?
DW: If direct joining would replace adhesives, it would mean re-planning our production lines. Manufacturing chains could be shortened and combined because the components can be manufactured, joined and further processed in-line.
LIA: What further research is needed in this area?
DW: Fully describing the interdependencies in the boundary layer of the metal-polymer joint exclusively with experimental research will be difficult. For this reason, we are currently working on a multiscale simulation approach to gain better understanding of the interdependencies. One main challenge is to transfer the effects of different surface characteristics (microscale) to strength predictions at component level (macroscale).
LIA: What could this research mean for the future?
DW: Direct joining in general allows redesigning joints in comparison to adhesive bonds. If, in addition, the capability of the joint can be predicted, manufacturing processes can be optimized and the confidence in those joints will be increased.
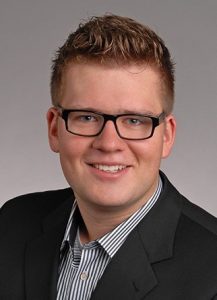
See Dominic present, “Precise Laser Structures as a Tool to Understand Metal-Polymer Joints“ (Authors: Dominic Woitun, Michael Roderus, Thilo Bein, Elmar Kroner) at the Laser Macroprocessing Conference Track on October 8, 2019. Register for ICALEO here: www.lia.org/conferences/icaleo
SOURCE: https://issuu.com/marketlia/docs/lia_today_augsept-2019/18?fr=sOTg0ZjIzMzQwOA